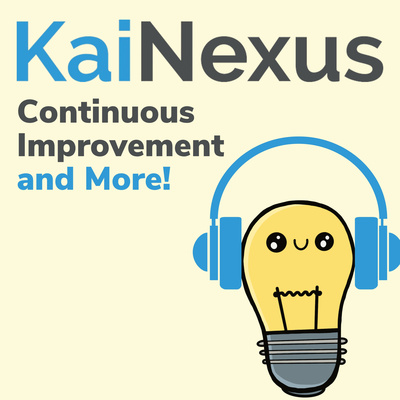
KaiNexus: Continuous Improvement, Leadership, and More
By KaiNexus
This podcast brings you information about continuous improvement best practices, employee engagement, lean, six sigma (and related improvement disciplines) and more. Join us as we explore the nuances of creating a culture of continuous improvement, no matter your level of expertise or your industry.
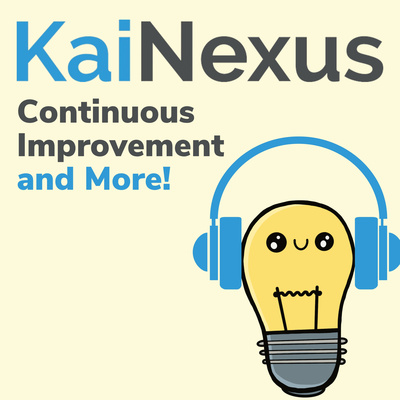
KaiNexus: Continuous Improvement, Leadership, and MoreMar 16, 2017
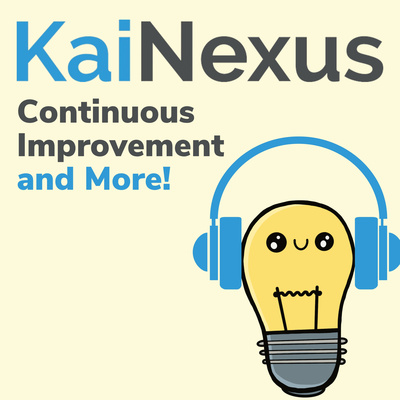
6 Essential Continuous Improvement Metrics That Matter
Maybe Albert Einstein was talking about continuous improvement when he said, “Not everything that can be counted counts, and not everything that counts can be counted.” We couldn’t have said it better ourselves.
Too often, we see organizations struggling to measure only those things that can be tied to a dollar amount and they, unfortunately, neglect the impact of ALL improvements. Let’s have a look at the top six ways to measure the impact of your organization’s improvement efforts.
![[Webinar] Lean: From Theory to Practice - One City’s (and Library’s) Lean Story… Abridged](https://d3t3ozftmdmh3i.cloudfront.net/production/podcast_uploaded_nologo400/1738065/1738065-1668561572420-df1dfb28a0f5.jpg)
[Webinar] Lean: From Theory to Practice - One City’s (and Library’s) Lean Story… Abridged
Presented by Elizabeth Chase View slides and video Join us for a look at how one library’s practice of Lean introduced a city to its benefits and informed the design of the 5th largest public library in Texas, a 158,000-square-foot library (in a repurposed rocket factory). Covering everything from creating a Lean training curriculum to specific examples of applied Lean fundamentals – with a detour into Vaccine site administration – this webinar has something for everyone interested in continuous improvement and/or libraries. Elizabeth Chase is the Material Services Manager for the Frisco Public Library. Elizabeth began her career with the City of Frisco in 2003. Before taking her current position, her roles at the Library included Adult Services Reference Librarian, Cataloger, and Senior Librarian. In the category of “other duties as assigned,” Elizabeth is a member of the Frisco Lean Team Steering Committee, which develops and implements Lean certification for City employees. Her primary role is teaching a 4-hour Lean fundamentals class to employees throughout the City and celebrating the improvements made as a result.
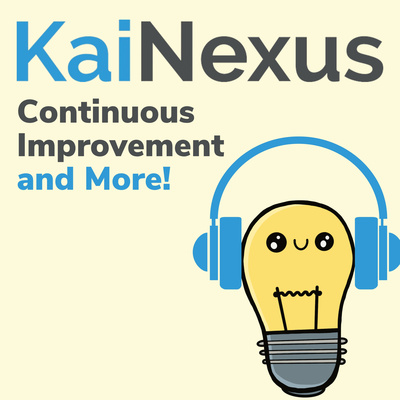
12 Characteristics of a Lean Organization
The renowned football coach and philosopher, Vince Lombardi, once said, “Perfection is unattainable, but if we chase perfection, we catch excellence.”
That’s the mindset of a Lean organization. There’s a bedrock belief that every process, investment, employee, or action should directly translate to value for the customer with no waste. That ideal is unattainable, of course, but Lean organizations try to get close to it every day, and in doing so, reach a level of success that their competitors can only envy. Every Lean organization is unique, but there are some core qualities that they tend to have in common.
![[Preview] Lean: From Theory to Practice, Webinar by Elizabeth Chase](https://d3t3ozftmdmh3i.cloudfront.net/production/podcast_uploaded_nologo400/1738065/1738065-1668561572420-df1dfb28a0f5.jpg)
[Preview] Lean: From Theory to Practice, Webinar by Elizabeth Chase
Join Mark Graban as he hosts Elizabeth Chase to preview her webinar...
April 24 from 1:00 pm - 2:00 pm ET
Presented by Elizabeth Chase
One City’s (and Library’s) Lean Story… Abridged
Join us for a look at how one library’s practice of Lean introduced a city to its benefits and informed the design of the 5th largest public library in Texas, a 158,000-square-foot library (in a repurposed rocket factory).
Covering everything from creating a Lean training curriculum to specific examples of applied Lean fundamentals – with a detour into Vaccine site administration – this webinar has something for everyone interested in continuous improvement and/or libraries.
Attendees will be able to ask as many questions that dive into specific details as time allows.
Elizabeth Chase is the Material Services Manager for the Frisco Public Library.
Elizabeth began her career with the City of Frisco in 2003. Before taking her current position, her roles at the Library included Adult Services Reference Librarian, Cataloger, and Senior Librarian.
In the category of “other duties as assigned,” Elizabeth is a member of the Frisco Lean Team Steering Committee, which develops and implements Lean certification for City employees. Her primary role is teaching a 4-hour Lean fundamentals class to employees throughout the City and celebrating the improvements made as a result.
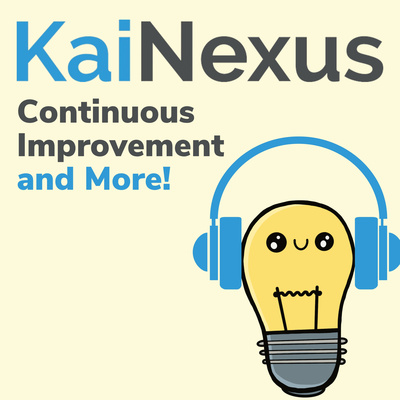
6 Steps to Continuous Improvement in the Automotive Industry 6 Steps to Continuous Improvement in the Automotive Industry
Find the blog post and the infographic
Written by Danielle Yoon, read by Mark Graban.
The post starts:
Manufacturers of all kinds seek to achieve continuous quality improvement because it ensures the consistency of products delivered to customers and protects against the competition. It also paves the path to compliance with industry-specific standards. This is crucial in the automotive sector because defective vehicle parts may lead to expensive recalls—or worse, accidents that cost lives.
Fortunately, continuous improvement has a long history in automotive manufacturing. Many of the tools and techniques widely used by organizations worldwide were explicitly developed to ensure the quality and efficiency of automotive manufacturing. Toyota was a pioneer of many of the CQI approaches used today. Whether you are using language like CQI, TQM, Lean, TPS, or Lean Six Sigma, these approaches described below still apply.
As you might imagine, the benefits of a successful continuous improvement program are significant, including:
6 Steps to Continuous Improvement in the Automotive Industry
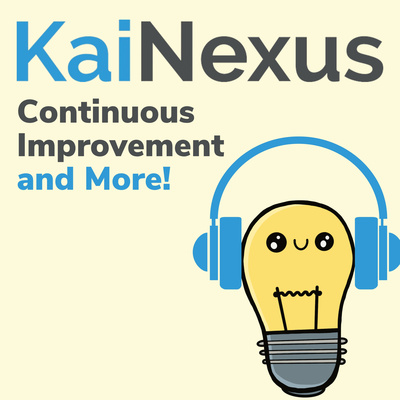
Greg Jacobson and Mark Graban Chat About KaiNexicon, the Kainexus User Conference, and More
Welcome to the KaiNexus Continuous Improvement Podcast. Today, we're excited to host Greg Jacobson, a lean thinker, and an inspiring visionary who has made significant strides in propagating the lean approach in the healthcare sector and beyond.
In this captivating dialogue, Mark Graban helps unravel the remarkable journey of Greg, highlighting his deep-rooted dedication to continuous improvement that stretches back to his early days in his mother's tuxedo shop.
Unfolding the chapters of Greg's extraordinary journey, we learn about the inception of KaiNexus, which came to life from the chaos of email clutter, evolving to become a robust system that fosters improvement and efficiency. Greg's story serves as a testament to the far-reaching influence of a single individual's dedication to constant betterment, potentially catalyzing a revolution in the industry by propelling productivity and quality of care forward.
![[Webinar] Developing Coaching Skills: Mine, Yours, Ours with Tracy Defoe](https://d3t3ozftmdmh3i.cloudfront.net/production/podcast_uploaded_nologo400/1738065/1738065-1668561572420-df1dfb28a0f5.jpg)
[Webinar] Developing Coaching Skills: Mine, Yours, Ours with Tracy Defoe
Presented by Tracy Defoe
How do you develop coaching skills in yourself and others? Why would you want to?
Everyone who manages people is asked to coach. Most of us think we are good at it. If you were lucky enough to learn how to develop and coach people because you were coached well from the start of your career, you are unusual. Most of us have to learn a new, quiet way of working with people to coach and develop them.
Join kata coach Tracy Defoe for her ideas on developing coaching skills the Toyota Kata way, based on years of personal and group experiential learning experiments.
This webinar is a preview of a deep dive Tracy is facilitating at the upcoming Kata Summit, KataCon10, coming up in April 2024.
Tracy Defoe is an adult educator specializing in learning at work. About ten years ago she started coaching to develop a scientific mindset in people improving their processes at work using the Improvement and Coaching Kata detailed in Mike Rother's Toyota Kata books. She is a cofounder of the global women's group Kata Girl Geeks, cofounder of Kata School Cascadia, and a facilitator with Tilo Schwarz's Kata Coaching Dojo Masterclass.
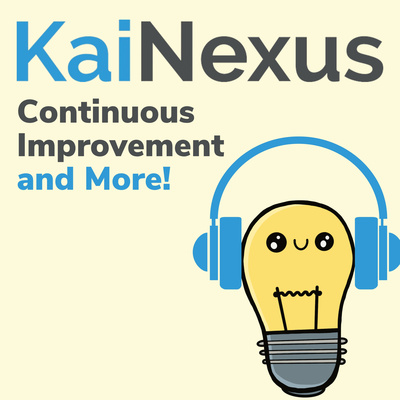
The 5 M’s of Kaizen for Effective Management
We often describe Kaizen as a way of looking at the world rather than a prescription for how to achieve positive change. Kaizen thinkers seek to make small changes to operations daily in search of higher quality, more efficiency, and less waste. But because the concept of Kaizen is so philosophical, it can be a challenge for people new to the idea to understand what it means in practical terms.
One useful tool for training managers to adopt the Kaizen mindset is called the 5 M’s. By consistently examining the 5 M’s, managers will be able to recognize when something in a process is not working and improve efficiency and profitability. This model can be used for risk mitigation, addressing safety issues, and improving quality. It can be used right alongside other Kaizen techniques such as the 5 Whys, 5S, and Gemba walks.
- Humanpower
- Machines
- Materials
- Methods
- Measurements
![[Webinar Preview] Developing Coaching Skills: Mine, Yours, Ours - with Tracy Defoe](https://d3t3ozftmdmh3i.cloudfront.net/production/podcast_uploaded_nologo400/1738065/1738065-1668561572420-df1dfb28a0f5.jpg)
[Webinar Preview] Developing Coaching Skills: Mine, Yours, Ours - with Tracy Defoe
To be presented March 21 from 1:00 pm - 2:00 pm ET This is a quick preview where host Mark Graban, a senior advisor with KaiNexus, chats with webinar presenter Tracy Defoe.
Registration Link Webinar Description: How do you develop coaching skills in yourself and others? Why would you want to? Everyone who manages people is asked to coach. Most of us think we are good at it. If you were lucky enough to learn how to develop and coach people because you were coached well from the start of your career, you are unusual. Most of us have to learn a new, quiet way of working with people to coach and develop them. Join kata coach Tracy Defoe for her ideas on developing coaching skills the Toyota Kata way, based on years of personal and group experiential learning experiments. This webinar is a preview of a deep dive Tracy is facilitating at the upcoming Kata Summit, KataCon10, coming up in April 2024. Tracy Defoe is an adult educator specializing in learning at work. About ten years ago she started coaching to develop a scientific mindset in people improving their processes at work using the Improvement and Coaching Kata detailed in Mike Rother's Toyota Kata books. She is a cofounder of the global women's group Kata Girl Geeks, cofounder of Kata School Cascadia, and a facilitator with Tilo Schwarz's Kata Coaching Dojo Masterclass.
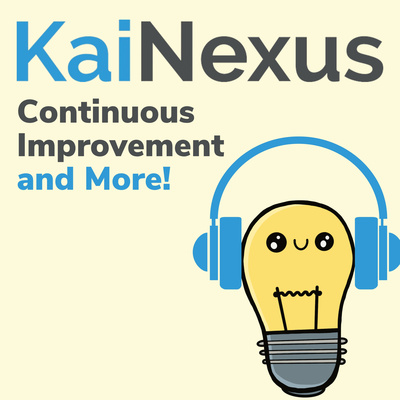
How Pella Regional Medical Center Benefits from KaiNexus
Visit the KaiNexus YouTube Channel
In this episode, we hear three clips with Tory Schrock, Director of Organizational Excellence at Pella Regional Health Center.
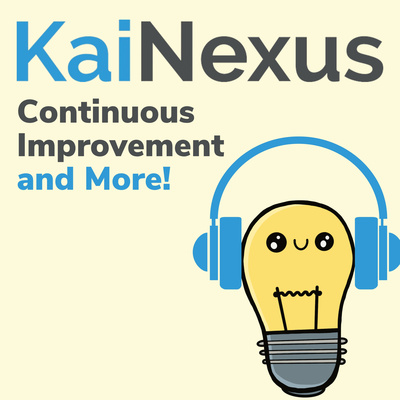
Lean Waste Reduction Strategies and Real-Life Examples
Ecologists and other environmentally aware people often talk about the goal of "Zero Waste." But, of course, that's an outstanding goal for business as well.
Reducing waste is at the heart of the Lean business methodology. The purpose of Lean is to spend more of your time creating value for customers by reducing or eliminating everything that does not produce value (AKA the waste). Value can take the form of finished goods, services, or information. To make it easier to identify waste in business processes, Lean practitioners target eight specific types of waste.
Although the Lean approach originated in manufacturing, it is used in almost every sector. Strikingly the eight wastes are common across industries, including software development, construction, healthcare, and education. Although it is not as apparent as it may be on a factory floor, the set of tasks and activities performed in any sector creates a production process that ultimately provides value to a customer.
While some of the wastes are self-explanatory, others are more difficult to recognize. This post aims to help by giving a few examples of each type of waste in various businesses. Hopefully, they will help you think about how waste may be occurring in your operations and how to begin designing processes that minimize it. Of course, the people who are most likely to find and correct waste are the process operators, so it is a good idea to share these examples with them and provide a way for each employee to submit opportunities for improvement.
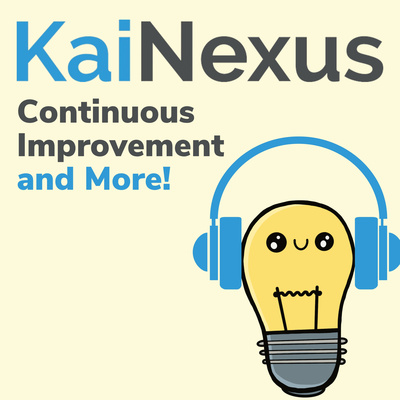
10 Continuous Improvement Questions to Ask in Every Interview
Companies dedicated to the practice of continuous improvement invest a lot of time and resources into training their employees and creating a culture centered around positive change. One way to make this easier and to smooth the path to improvement is to hire people who already have the right mindset.
Bringing up continuous improvement during the initial interview and throughout the hiring process lets the applicant know how important it is to your organization, and helps you weed out people who will be resistant to feedback and change.
If you ask the right questions, you can get a pretty good idea of whether the candidate is likely to be a good fit in your improvement culture and someone that the rest of the team will gladly welcome.
Here are some ideas of what to ask...
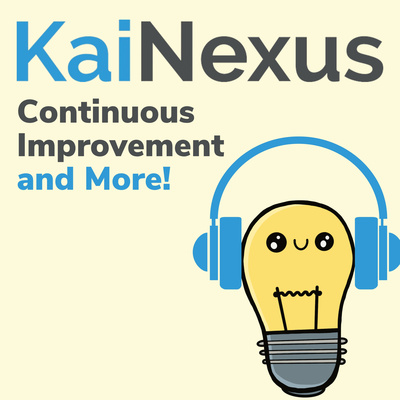
Central Principles of the Continuous Improvement Model
Written by Maggie Millard, read by Mark Graban
Businesses use a host of methodologies to bring structure to the process of identifying and acting upon opportunities for improvement. You may be familiar with Six Sigma, Kaizen, Lean, Toyota Production System, and others. Although these methodologies differ, the foundation of each of them is the continuous improvement model.
The continuous improvement model reflects the idea that organizations should constantly implement incremental improvements to services, products, and processes. The approach applies to every industry and size of business. Several central principles guide the continuous improvement model.
![Apply Operations Science to Accelerate Success Now [Webinar Recording] Ed Pound](https://d3t3ozftmdmh3i.cloudfront.net/production/podcast_uploaded_nologo400/1738065/1738065-1668561572420-df1dfb28a0f5.jpg)
Apply Operations Science to Accelerate Success Now [Webinar Recording] Ed Pound
Operations science describes the fundamental relationships that drive operations performance. However, the concepts are not widely understood or applied properly. Join us for this webinar with Ed Pound, Managing Director of the Operations Science Institute to:
- Learn a fundamental, expensive problem that plagues nearly all organizations yet is widely unknown
- Participate in an exercise to see if this problem affects your organization
- Learn some basic concepts of operations science and how the field can be used to accelerate your organization’s success right now, with your existing people and technology. No capex needed.
Ed Pound is the Managing Director of the Operations Science Institute, lead author of the book "Factory Physics for Managers," and co-author of the upcoming book "Applied Operations Science." Ed has over 35 years of experience managing, coaching, and training in operations across many different industries and countries and in businesses large and small.
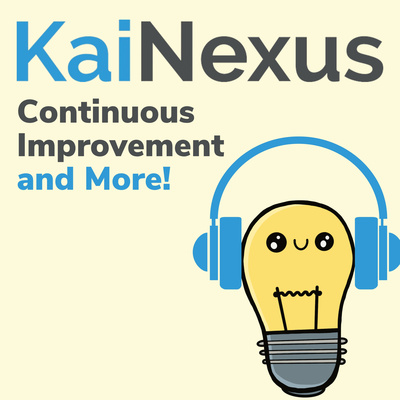
Inspiring Improvement: Our Guiding Values at KaiNexus -- Greg Jacobson and Jeff Roussel Discuss
From this video, Jeff Roussel (chief revenue officer) and Greg Jacobson (co-founder and CEO) discuss the culture at KaiNexus.
Learn more about jobs at KaiNexus
In this enlightening episode of the KaiNexus Continuous Improvement Podcast, join Jeff Roussel and Greg Jacobson for a deep dive into the unique corporate ethos of Kinexis. Discover how this dynamic company has etched out its colossal success through the shared formulation and embodiment of collective core values. Rather than a top-down approach, KaiNexus methodically identified fundamental behaviors through employee interactions that came to define their organization. Their culture vividly narrates a story of shared beliefs where every policy adopted and decision made is a tribute to their core values. Let’s explore how they've shaped their environment, where principles aren't simply stated words, but an integral part of the everyday actions.
Take a journey revealing how the cornerstone of teamwork contributes significantly to KaiNexus's triumphs. Understanding that individual efforts culminate in extraordinary feats when synchronized into a collective endeavor is their core mantra. Discover how Kinexis has cultivated a workplace where collaboration and collective success are at the heart of every initiative. A discussion featuring their outlook on kindness as a strength, focusing on customer needs, and the embedding of trust will help listeners understand how the company's values contribute to a nurturing and respectful business ethos, while also delivering superior service to its clientele.
![[Webinar Preview] Apply Operations Science to Accelerate Success Now - Ed Pound](https://d3t3ozftmdmh3i.cloudfront.net/production/podcast_uploaded_nologo400/1738065/1738065-1668561572420-df1dfb28a0f5.jpg)
[Webinar Preview] Apply Operations Science to Accelerate Success Now - Ed Pound
Learn more and register here February 6 from 1:00 pm - 2:00 pm ET Presented by Ed Pound, joined by Mark Graban from KaiNexus for a preview discussion in this episode. Operations science describes the fundamental relationships that drive operations performance. However, the concepts are not widely understood or applied properly. Join us for this webinar with Ed Pound, Managing Director of the Operations Science Institute to: Learn a fundamental, expensive problem that plagues nearly all organizations yet is widely unknown Participate in an exercise to see if this problem affects your organization Learn some basic concepts of operations science and how the field can be used to accelerate your organization’s success right now, with your existing people and technology. No capex needed Ed Pound is the Managing Director of the Operations Science Institute, lead author of the book "Factory Physics for Managers," and co-author of the upcoming book "Applied Operations Science." Ed has over 35 years of experience managing, coaching, and training in operations across many different industries and countries and in businesses large and small.
![A Poka-Yoke Primer: Mistake-Proofing and Error Reduction [Webinar]](https://d3t3ozftmdmh3i.cloudfront.net/production/podcast_uploaded_nologo400/1738065/1738065-1668561572420-df1dfb28a0f5.jpg)
A Poka-Yoke Primer: Mistake-Proofing and Error Reduction [Webinar]
YouTube Link: https://www.youtube.com/watch?v=B9A0Zlf_048&ab_channel=KaiNexus
As presented by John Grout on 1/17/24. Hosted by Mark Graban of KaiNexus.
This webinar is a 60-minute primer into mistake-proofing (a.k.a. poka-yoke). Information about the basics of mistake-proofing, why people make mistakes, and how to start the process of reducing mistakes will be presented in a fast-moving and entertaining format.
Objectives:
- Build awareness of mistake-proofing
- Introduce a concise presentation format: “pecha kucha," with 20 slides x 0:20 seconds each = 6:40 minutes (we’ll do two of these with discussion in between).
- What is mistake-proofing?
- Include lots of examples
- Why do people err?
- How can design eliminate errors?
- Next steps in implementation
John Grout is the David C. Garrett Jr. Professor, former dean, and award-winning teacher in the Campbell School of Business at Berry College. Dr. Grout has researched lean supply chain management and mistake-proofing (a.k.a. Poka-Yoke) extensively and published numerous articles on the topic. John was awarded the Shingo Prize for his paper, “The Human Side of Mistake-Proofing” with Douglas Stewart. John has also consulted with a large variety of firms to mistake-proof their processes.
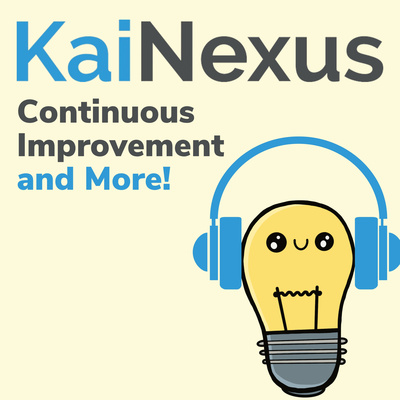
Examples of the 8 Wastes of Lean Across Industries
One of the most critical concepts in Lean organizations is the idea that it is essential to eliminate waste. Why is it so central to the practice of Lean? The principles of Lean say that the ultimate goal is to provide perfect customer value. Anything that provides value to the customer is preserved. Everything else is considered waste. Some waste is inevitable due to physical constraints, regulations, or safety considerations. Still, most organizations find that they are engaged in many unnecessary activities and use more resources than is strictly required.
If you are striving to become a Lean organization, waste elimination is probably near the top of your list. Lean practitioners have identified particular types of waste, known collectively as the 8 Wastes of Lean. Certain types of waste are easy to spot and fix, while others are more difficult to detect.
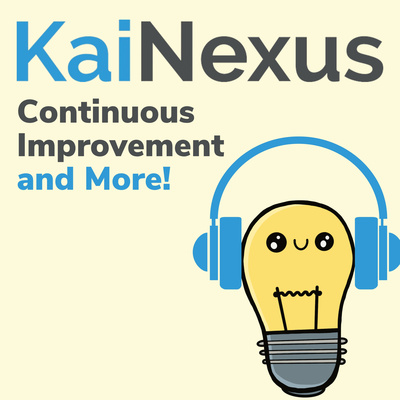
Webinar Preview: A Poka-Yoke Primer: Mistake-Proofing and Error Reduction with John Grout
Register for the webinar here In this video, host Mark Graban from KaiNexus talks with John Grout about his upcoming webinar to be held on January 17th. This webinar is a 60-minute primer into mistake-proofing (a.k.a. poka-yoke). Information about the basics of mistake-proofing, why people make mistakes, and how to start the process of reducing mistakes will be presented in a fast-moving and entertaining format. Objectives: Build awareness of mistake-proofing Introduce a concise presentation format: “pecha kucha," with 20 slides x 0:20 seconds each = 6:40 minutes (we’ll do two of these with discussion in between). What is mistake-proofing? Include lots of examples Why do people err? How can design eliminate errors? Next steps in implementation About the Presenter: John Grout John Grout is the David C. Garrett Jr. Professor, former dean, and award-winning teacher in the Campbell School of Business at Berry College. Dr. Grout has researched lean supply chain management and mistake-proofing (a.k.a. Poka-Yoke) extensively and published numerous articles on the topic. John was awarded the Shingo Prize for his paper, “The Human Side of Mistake-Proofing” with Douglas Stewart. John has also consulted with a large variety of firms to mistake-proof their processes.
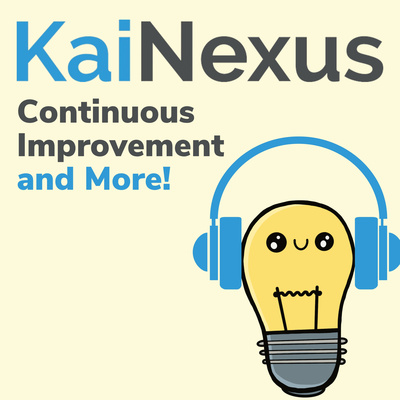
11 Steps to an Effective Gemba Walk
Gemba walks are an increasingly popular management technique. By visiting the place where work is done, leaders gain valuable insight into the flow of value through the organization and often uncover opportunities for improvement and learn new ways to support employees. The approach is a collaborative one, with employees providing details about what is done and why.
Great results depend on thoughtful planning, execution, and follow-up. Here are the most important steps you can take to ensure that your next Gemba walk is successful.
Written by Kade Jansson and read by Mark Graban
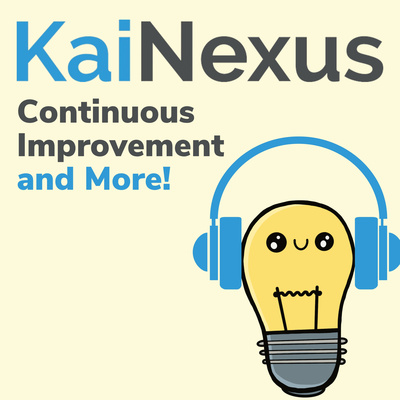
5 Principles of a High Reliability Organization (HRO)
A high-reliability organization (HRO) is an organization that has succeeded in avoiding catastrophes despite a high level of risk and complexity. Specific examples that have been studied, most famously by researchers Karl Weick and Kathleen Sutcliffe, include nuclear power plants, air traffic control systems, and naval aircraft carriers. Recently healthcare organizations have moved to adopt the HRO mindset as well. In each case, even a minor error could have catastrophic consequences.
Yet, adverse outcomes in these organizations are rare. How is that possible?
Written by Greg Jacobson, read by Mark Graban
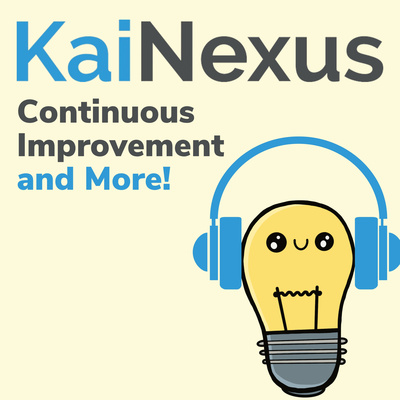
When Being Right is the Wrong Strategy for Change - Mark Graban from KaiNexus
Watch Mark Graban's keynote entitled "When Being Right is the Wrong Strategy for Change" from the 2018 KaiNexus User Conference to learn how you can become a better leader of continuous improvement. Slides and More: https://www.markgraban.com/kainexus2018/ Join Mark Graban, an acclaimed author and consultant, in his enlightening keynote address at the 2018 KaiNexus User Conference. In this presentation, titled "When Being Right is the Wrong Strategy for Change," Mark delves into the intricate dynamics of leadership and change management. Drawing from his vast experience and insights, he explores the often-overlooked psychological aspects of leading continuous improvement in any organization. Mark challenges conventional wisdom by arguing that being factually correct is not always the most effective way to inspire change. Instead, he introduces a more nuanced approach that balances knowledge with empathy and understanding. Through a series of engaging slides, Mark illustrates the transition from a directive style of leadership (akin to a 'cop') to a more collaborative and counseling approach. He emphasizes the significance of understanding the 'why' behind actions and the power of asking others why they would want to engage in change, thereby fostering a more inclusive and motivational environment. This presentation is particularly valuable for leaders looking to drive sustainable change. It provides actionable insights into the psychology of change, motivational interviewing techniques, and the importance of resisting the 'righting reflex' — the natural tendency to correct others. Mark showcases how to create an atmosphere that encourages open dialogue, self-motivation, and a shared vision for change. By the end of this keynote, viewers will gain a deeper understanding of: - The difference between enforcing compliance and fostering genuine change. - Strategies to move from being a 'cop' to a 'coach' to a 'counselor' in leadership roles. - The concept of Motivational Interviewing and its application in leadership and change management. - Techniques to engage in more effective conversations about change and resistance. - Understanding and navigating one's own ambivalence and that of others in the context of change. Discover more about Mark Graban and his work by visiting [MarkGraban.com](https://www.markgraban.com/) and [LeanBlog.org](https://www.leanblog.org/). For additional resources related to this presentation, please visit [MarkGraban.com/KaiNexus2018](https://www.markgraban.com/KaiNexus20.... Don't miss this opportunity to enhance your leadership skills and approach to change management. Watch now and start your journey towards more impactful and empathetic leadership!
![[Webinar] Engaging Senior Leaders to Accelerate Your Continuous Improvement Program](https://d3t3ozftmdmh3i.cloudfront.net/production/podcast_uploaded_nologo400/1738065/1738065-1668561572420-df1dfb28a0f5.jpg)
[Webinar] Engaging Senior Leaders to Accelerate Your Continuous Improvement Program
Watch video, download the PDF worksheet, and more
Presented by Stephanie Hill, Senior Lean Strategist at KaiNexus
Having worked as…
…a CI practitioner reporting to a CFO,
…a consultant and coach to executives and
…a Lean Strategist configuring software to meet executives’ needs,
Stephanie has learned that senior leaders are the influencers of any organization - able to make or break a CI program and culture.
Attendees will:
- Gain clarity on the need for executive buy-in and engagement.
- Learn three considerations before engaging senior leaders in CI.
During the session, attendees will have the opportunity to reflect on their gaps in building relationships with their senior leaders. Participants will walk away with a plan to increase executive engagement.
Stephanie Hill is a Senior Lean Strategist with KaiNexus and owner of Light Bulb Moment Consulting. She has over 23 years of experience applying Lean to various industries, including legal, manufacturing, retail, insurance, healthcare, and government. She has certifications in Strategic Human Resources Leadership and Scaled Agile, a Master Black Belt in Lean Six Sigma, a master’s degree in Public Health, and a bachelor's degree in Chemistry. She lives near Columbus, Ohio, and enjoys building LEGO sets, dancing, and traveling. She is also preparing to publish her first book, "A Life of Learning: Lessons in Leadership from Raising a Boy with Autism."
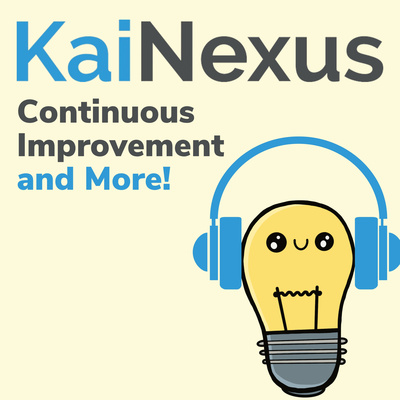
Why You Should Use KaiNexus as Your A3 Software Instead of SharePoint, Excel, or Other Solutions
See the video: https://youtu.be/8XhR8n8sn8M
Learn more about KaiNexus: https://kainexus.com/
Matt Banna: My name's Matt Banna, and I'm an enterprise account executive at KaiNexus. Oftentimes organizations come to us because they're having challenges managing their A3s. They don't have visibility into the work that's happening, who's doing what, and when are things on track or off track? And ultimately, how are these A3s impacting their organizational goals? They've tried to solve these challenges through tools that aren't fit for purpose, like Excel or PowerPoint, or uploading things into a SharePoint drive or even creating homegrown systems. Matt Banna: What they've found is that once things get saved into SharePoint, they go into some sort of black hole. And nobody ever sees the results of those A3s. Or if they go to some sort of project management solution. Those A3s aren't shaped like A3s. Matt Banna: And so all the work that they've done to teach the A3 problem solving methodology goes out the window. Because the format of how people are solving those problems in that tool doesn't look like the format that they've been taught. But we'll work together to configure your A3 in KaiNexus to mirror the standard that you've built and that you've taught within your organization. In this example we have configured, you can see a background and a current condition countermeasures a way to prioritize this project against others. You can use it to assign tasks directly to people that will automatically notify them once they've been assigned, or that work becomes overdue. Matt Banna: Categorize this work however you want with some sort of priority, or connect it to strategic initiatives. Add in root cause like Five Whys or Fishbones, attach before and after pictures or any approvals that are needed once this A3 is actually completed, simply going into the resolution to say what happened? What was the outcome of this project? Was it qualitative or quantitative, such as some sort of quality or safety change? Or maybe there was some sort of cost savings where you can say how much you saved, how often, and then be able to report on that later throughout the organization. Matt Banna: Managing your A3s and KaiNexus gives visibility to the organization at multiple levels, gives visibility of the work that's happening to different team members so they can share best practices or make sure that they're not working on duplicate efforts. It gives visibility into your CI team so that they can more effectively coach or congratulate people who are doing good work, and it gives more visibility to executives so they can track the impact of the work that's happening. And ultimately, how is that affecting your organizational goals?
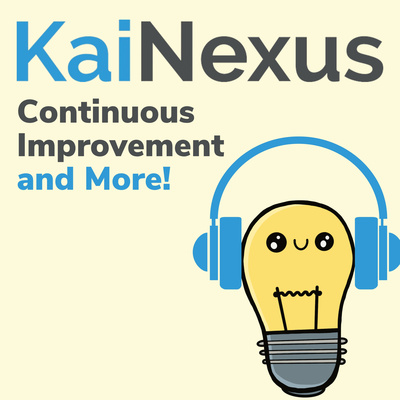
Mark and Greg on Thanksgiving Processes, the AME Conference, Technology, Favorite Books
Harness the power of continuous improvement (CI) as it nods to many facets of both personal life and business in our KaiNexus Continuous Improvement Podcast featuring speakers Mark Graban and Greg Jacobson. Get a closer look at the impact of CI on daily activities with an interesting focus on cooking a Thanksgiving turkey and see how the establishment of standard operating procedures (SOPs) can aid in safety and efficiency.
Learn more about KaiNexus: https://kainexus.com/
In addition, the podcast delves into the critical role of checklists and SOPs in complex tasks, using the turkey preparation as a case study. Tune in and explore how technology integration can further enhance safety and cooking outcomes. Understand the application of CI principles in scheduling the timing of various festive dishes for stress-free holiday meals, on par with standard industrial processes. The takeaway from this podcast emphasizes the profound influence of CI on personal traditions and professional progress.
Books and Resources for Aspiring Leaders
Educating oneself on effective leadership practices can significantly transform how one goes about influencing behavior and instituting lasting change. Books like Crucial Influence: Leadership Skills to Create Lasting Behavior Change offer guidance on how to lead with intention and purpose.
Other notable texts include:
Never Lose an Employee Again by Joey Coleman, which focuses on employee retention through onboarding and integration into company culture.
Drive by Daniel H. Pink, that delves into human motivation and the factors that compel us to excel in what we do.
Atomic Habits by James Clear, emphasizing the power of small consistent changes over time.
Finally, foundational reads like Kaizen by Masaaki Imai remind leaders of the roots of continuous improvement and lean thinking.
![[Preview] Engaging Senior Leaders to Accelerate Your Continuous Improvement Program - Stephanie Hill](https://d3t3ozftmdmh3i.cloudfront.net/production/podcast_uploaded_nologo400/1738065/1738065-1668561572420-df1dfb28a0f5.jpg)
[Preview] Engaging Senior Leaders to Accelerate Your Continuous Improvement Program - Stephanie Hill
Register here for the live event
December 5 from 1:00 pm - 2:00 pm ET Presented by Stephanie Hill, Senior Lean Strategist at KaiNexus Having worked as… …a CI practitioner reporting to a CFO, …a consultant and coach to executives and …a Lean Strategist configuring software to meet executives’ needs,
Stephanie has learned that senior leaders are the influencers of any organization - able to make or break a CI program and culture. Attendees will: - Gain clarity on the need for executive buy-in and engagement. - Learn three considerations before engaging senior leaders in CI.
During the session, attendees will have the opportunity to reflect on their gaps in building relationships with their senior leaders. Participants will walk away with a plan to increase executive engagement. About the Presenter: Stephanie Hill, Senior Lean Strategist Stephanie Hill is a Senior Lean Strategist with KaiNexus and owner of Light Bulb Moment Consulting. She has over 23 years of experience applying Lean to various industries, including legal, manufacturing, retail, insurance, healthcare, and government. She has certifications in Strategic Human Resources Leadership and Scaled Agile, a Master Black Belt in Lean Six Sigma, a master’s degree in Public Health, and a bachelor's degree in Chemistry. She lives near Columbus, Ohio, and enjoys building LEGO sets, dancing, and traveling. She is also preparing to publish her first book, "A Life of Learning: Lessons in Leadership from Raising a Boy with Autism."
![No More Flavor of the Month! Learn How To Deliver Sustainable Change [Webinar Recording Lynn Kelley]](https://d3t3ozftmdmh3i.cloudfront.net/production/podcast_uploaded_nologo400/1738065/1738065-1668561572420-df1dfb28a0f5.jpg)
No More Flavor of the Month! Learn How To Deliver Sustainable Change [Webinar Recording Lynn Kelley]
Recorded November 7 Presented by D. Lynn Kelley, Ph.D. Co-Author of Change Questions: A Playbook for Effective and Lasting Organizational Change The book "Change Questions" unlocks the secrets of sustainable organizational change by asking key questions that deliver a customized approach for change that is just right for your specific initiative and organization. You will be given access to the free digital workbook, which is a fillable PDF that you can save, use, and reuse in your future change activities. After this webinar, you will be able to develop a customized implementation plan for a change initiative that integrates the topics listed below: a. Purpose b. Design, Do, and Improve the Work of the Change c. Capability Building and Employee Engagement d. Management System and Leadership e. Culture Following a career highlighted by leadership roles in engineering, supply chain, and continuous improvement in various industries, Kelley retired from Union Pacific Railroad in 2018. Now serving as a senior advisor to BBH Capital Partners, she assists in sourcing, investment evaluation, transaction execution, and providing post-investment oversight to the firm’s portfolio companies. At Union Pacific, she was senior vice president of supply chain and continuous improvement. She was also the executive co-owner of the company’s innovation program. Before joining Union Pacific, Kelley was vice president of operational excellence, an officer and a member of the executive leadership team at Textron. Kelley holds a PhD in evaluation and research and taught undergraduate and graduate statistics courses. Before becoming a professor, she held the positions of executive vice president and chief operating officer of Doctors Hospital in Detroit.
![[Preview] No More Flavor of the Month! Learn How To Deliver Sustainable Change - Lynn Kelley](https://d3t3ozftmdmh3i.cloudfront.net/production/podcast_uploaded_nologo400/1738065/1738065-1668561572420-df1dfb28a0f5.jpg)
[Preview] No More Flavor of the Month! Learn How To Deliver Sustainable Change - Lynn Kelley
Register for the webinar D. Lynn Kelley, Ph.D. joins Mark Graban, senior advisor with KaiNexus, to preview her webinar presentation. November 7 from 1:00 pm - 2:00 pm ET Presented by D. Lynn Kelley, Ph.D. Co-Author of "Change Questions: A Playbook for Effective and Lasting Organizational Change" The book "Change Questions" unlocks the secrets of sustainable organizational change by asking key questions that deliver a customized approach for change that is just right for your specific initiative and organization. You will be given access to the free digital workbook, which is a fillable PDF that you can save, use, and reuse in your future change activities. After this webinar, you will be able to develop a customized implementation plan for a change initiative that integrates the topics listed below: a. Purpose b. Design, Do, and Improve the Work of the Change c. Capability Building and Employee Engagement d. Management System and Leadership e. Culture Following a career highlighted by leadership roles in engineering, supply chain, and continuous improvement in various industries, Kelley retired from Union Pacific Railroad in 2018. Now serving as a senior advisor to BBH Capital Partners, she assists in sourcing, investment evaluation, transaction execution, and providing post-investment oversight to the firm’s portfolio companies. At Union Pacific, she was senior vice president of supply chain and continuous improvement. She was also the executive co-owner of the company’s innovation program. Before joining Union Pacific, Kelley was vice president of operational excellence, an officer and a member of the executive leadership team at Textron. Kelley holds a PhD in evaluation and research and taught undergraduate and graduate statistics courses. Before becoming a professor, she held the positions of executive vice president and chief operating officer of Doctors Hospital in Detroit.
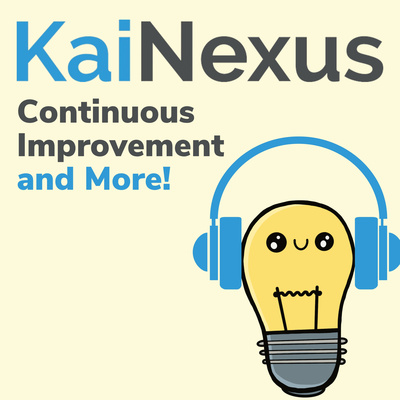
Mark Graban & Greg Jacobson on Continuous Improvement and Customer Experience Design
Get ready for another insightful episode of KaiNexus Continuous Improvement Podcast with our esteemed hosts, Mark Graban and Greg Jacobson. Drawing from the Toyota Production System, this episode dives deep into the principles of continuous improvement, offering valuable lessons relevant to various sectors beyond just manufacturing.
Unravel the central principle of respect for people and customers as Mark and Greg discuss the substantial impact that this simple component can have on customer satisfaction and rapport. It's not just about delivering service; it’s about demonstrating recognition and appreciation. Delve into exciting, relatable narratives that emphasize the significance of respect in our daily interactions and how it lays the groundwork of undeniably fruitful relationships.
LINKS:
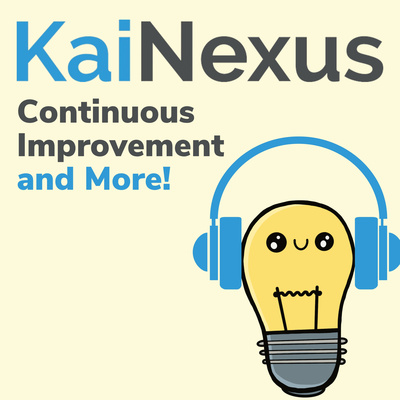
The Importance of Trust in Continuous Improvement [Webinar by Colleen Soppelsa)
Presented by Colleen Soppelsa, a Lean and Six Sigma Transformation Leader with 20+ years of experience Charles Feltman defines trust as "choosing to risk making something you value vulnerable to another person's actions." This webinar will delve into how lack of trust from the employee experience degrades their relationships with management, coworkers, and their jobs, leading to an environment unprepared for Lean methodology. You will learn about approaches outside the traditional Lean framework to change the DNA from the middle. Colleen Soppelsa is a Lean and Six Sigma Transformation Leader with 20+ yrs experience across the Automotive (Toyota), Aviation (GEA) and Aerospace & Defense (L3H) Industries. She has been committed to creating breakthrough thinking environments based on the "Respect for People" principle specifically in the area of Trust as a non-negotiable for a Lean Culture.
![[Preview] The Importance of Trust in Continuous Improvement, a Webinar by Colleen Soppelsa](https://d3t3ozftmdmh3i.cloudfront.net/production/podcast_uploaded_nologo400/1738065/1738065-1668561572420-df1dfb28a0f5.jpg)
[Preview] The Importance of Trust in Continuous Improvement, a Webinar by Colleen Soppelsa
October 17 from 1:00 pm - 2:00 pm ET
Presented by Colleen Soppelsa, a Lean and Six Sigma Transformation Leader with 20+ years of experience
Charles Feltman defines trust as "choosing to risk making something you value vulnerable to another person's actions." This webinar will delve into how lack of trust from the employee experience degrades their relationships with management, coworkers, and their jobs, leading to an environment unprepared for Lean methodology. You will learn about approaches outside the traditional Lean framework to change the DNA from the middle.
Colleen Soppelsa is a Lean and Six Sigma Transformation Leader with 20+ yrs experience across the Automotive (Toyota), Aviation (GEA) and Aerospace & Defense (L3H) Industries. She has been committed to creating breakthrough thinking environments based on the "Respect for People" principle specifically in the area of Trust as a non-negotiable for a Lean Culture.
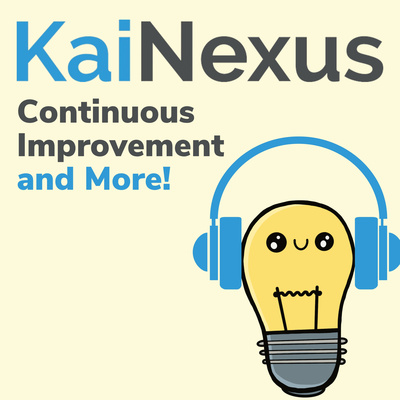
Remembering Chris Burnham, Our Friend and Colleague
In this episode, Greg Jacobson and Mark Graban share memories and stories of Chris Burnham, who passed away recently.
Greg and Mark talk about being guests on Chris's podcast, The Lean Leadership Podcast.
We answer two questions from the list of "rapid fire" questions that Chris would ask in his podcast:
- Do you have a Lean/Continuous improvement pet peeve/or what do you frequently see being applied or being done wrong?
- What do you consider the most important thing that you have learned in your career journey?!
Here is the webinar that Chris did for us as part of the KaiNexus series. And he was part of this panel discussion about virtual improvement.
We dedicate today's KaiNexus Continuous Improvement Podcast episode to a remarkable individual whose loss has been deeply felt within the Lean community. Chris Burnham, a Lean thinker, a podcast host, and a leader in the field, recently left us, creating a void which has been challenging to navigate. This episode serves as a tribute to Chris's life, his work, and his indelible influence on those fortunate enough to cross his path.
In addition to his brilliance as a Lean thinker, Chris's exemplary character shone through in his role as the host of the Lean Leadership Podcast. His hunger for knowledge and openness to new ideas defined many of his interactions. In 2015, Chris kickstarted his podcast series by inviting Mark Graban aboard as his inaugural guest - beginning a progressive journey through the realm of Lean thinking and practices.
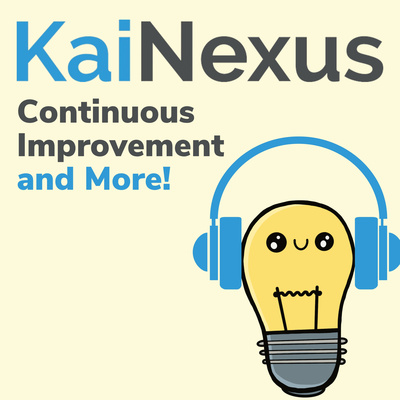
Webinar — Ask a CEO (Mark Parrish): Building Cultures of Commitment
Recording of a Sept 14 Webinar - Learn More, See Video
Presented by Mark Parrish
This webinar provides an exciting and unique opportunity to ask an experienced CEO questions about leadership, culture, and continuous improvement. We’ll be joined by Mark Parrish, a graduate of the United States Military Academy at West Point and the Massachusetts Institute of Technology. Mark is a six-time CEO at public, private and private equity companies, to include Igloo Products Corp. and the Stuart Dean Company, Inc.
Mark provides his audience world-class lessons in leadership and operational excellence gathered over three decades from within the "living laboratories" of myriad companies and industries. How can leaders create a company culture worthy of each and every employee’s full 100% commitment? How can the “business goal” of making a dollar co-exist with the “noble goal” of making a difference? How do we navigate the waters of trust, engagement, and organizational politics? Come "Ask the CEO" yourself.
The formal presentation will be brief – 15 minutes. The remainder of the hour will allow the audience to interact with Mark via moderated Q&A – submitted both in advance and during the session.
![[Preview] With Mark Parrish — Ask a CEO: Building Cultures of Commitment [Preview]](https://d3t3ozftmdmh3i.cloudfront.net/production/podcast_uploaded_nologo400/1738065/1738065-1668561572420-df1dfb28a0f5.jpg)
[Preview] With Mark Parrish — Ask a CEO: Building Cultures of Commitment [Preview]
Register in advance (or to view the recording) -- Ask a CEO: Building Cultures of Commitment
September 14th at 1 pm ET
Presented by Mark Parrish, hosted by Mark Graban
This webinar provides an exciting and unique opportunity to ask an experienced CEO questions about leadership, culture, and continuous improvement. We’ll be joined by Mark Parrish, a graduate of the United States Military Academy at West Point and the Massachusetts Institute of Technology. Mark is a six-time CEO at public, private and private equity companies, to include Igloo Products Corp. and the Stuart Dean Company, Inc.
Mark provides his audience world-class lessons in leadership and operational excellence gathered over three decades from within the "living laboratories" of myriad companies and industries. How can leaders create a company culture worthy of each and every employee’s full 100% commitment? How can the “business goal” of making a dollar co-exist with the “noble goal” of making a difference? How do we navigate the waters of trust, engagement, and organizational politics? Come "Ask the CEO" yourself.
The formal presentation will be brief – 15 minutes. The remainder of the hour will allow the audience to interact with Mark via moderated Q&A – submitted both in advance and during the session.
About Mark Parrish:
Mark Parrish is Managing Partner and co-founder of Parrish Partners, LLC, the twenty-year-old, southern California-based leadership and management consulting firm.
Previously, Mark was CEO, President, and Director of Igloo Products Corp., the 76-year-old, private equity owned, U.S.-based manufacturer of the iconic Igloo brand of commercial and consumer cooler and drinkware products. While in his role at Igloo, Mr. Parrish was named the Houston Business Journal’s “2017 Outstanding CEO.”
Immediately prior to joining Igloo, Mark was CEO, President, and Director of Stuart Dean Company, Inc., the 86-year-old, private family-owned, Manhattan-based international real estate restoration and preservation company. Stuart Dean customers include the Empire State Building, the White House, the Golden Gate Bridge, and Apple stores worldwide.
Mark has an accomplished record of leading organizational transformations of U.S.-based manufacturers and service providers. His contributions have yielded tremendous value creation with well-known consumer brands, such as Harley-Davidson and Simmons, and other industry leaders, including Ply Gem Windows, Interface, Inc., and Deceuninck North America, each world-class manufacturers known for their rapid product innovation.
Mark is a distinguished graduate of the United States Military Academy at West Point. During his ten years of uniformed service in Army Aviation, he served in five countries on three continents. As an AH-64 Apache pilot and Army “Top Gun,” he served in Operations Desert Shield/Storm, where he was awarded the Bronze Star and Air Medal for Valor. He later earned two Master of Science degrees in Engineering and Management from the Massachusetts Institute of Technology.
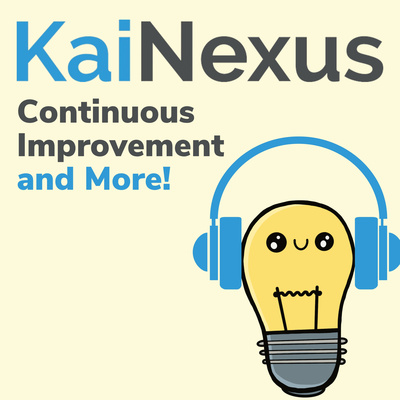
Noah Paratore: Why Did You Join KaiNexus? What Do You Do?
Today, Mark Graban is joined by Noah Paratore, a Senior Solutions Engineer at KaiNexus. Noah shares his story about why and when he joined KaiNexus as employee #19. Why does he love what the company stands for, including continuous improvement and helping him feel heard? How does he apply continuous improvement mindsets to everyday life, including relationships? Noah also discusses his progression of roles, being a "KaiNexpert," and the ongoing debate about who is "funniest in the gemba."
![Person-Centred Improvement - What Does it Look Like, and How Does it Fit with Lean? [Webinar]](https://d3t3ozftmdmh3i.cloudfront.net/production/podcast_uploaded_nologo400/1738065/1738065-1668561572420-df1dfb28a0f5.jpg)
Person-Centred Improvement - What Does it Look Like, and How Does it Fit with Lean? [Webinar]
August 15 from 1:00 pm - 2:00 pm ET
Presented by Seán Paul Teeling, Programme Director for the Professional Certificate and Graduate Certificate in Process Improvement in Health Systems at UCD Health Systems.
Lean is one of the most internationally popular process improvement methodologies around the world. Similarly, person-centred approaches have risen in popularity since the millennium with political and policy intentions now widely advocating that person-centredness should be at the heart of the health system. In this webinar, we discuss the first research internationally into the combined use of Lean and person-centred improvement approaches, lessons learnt, and how to be a person-centred improver in any industry or setting.
Learning objectives:
- Understand what is meant by person-centred improvement
- Identify the synergies between Lean and person-centred improvement
- Understand where person-centred improvement diverges from Lean and how to address it
- Be able to incorporate person-centred approaches into your Lean work
Seán Paul Teeling is the Programme Director for the Professional Certificate and Graduate Certificate in Process Improvement in Health Systems at UCD Health Systems. Prior to this, he worked as Lean Manager at the Mater Misericordiae University Hospital Dublin, working closely with the Hospital and the UCD School of Nursing, Midwifery and Health Systems on the development of the highly successful Process Improvement in healthcare programmes.
Seán Paul is an accredited facilitator of Person-centred Cultures in Healthcare. He completed his PhD with and is a member of, and honorary lecturer with, the Centre for Person-Centred Practice Research, Queen Margaret University, Edinburgh. He is also an affiliate of the Stanford Medicine Centre for Improvement, Stanford University, CA. His research is in the use of process and quality improvement methodologies in healthcare including the Model for Improvement, Lean, Six Sigma, Lean Six Sigma and Agile and in particular the influence and contribution of Process Improvement methodologies on Person-centred Cultures. In January 2011, he was appointed by the Minister for Health as a member of the Health Products Regulatory Authority Advisory Committee on Medical Devices, on which he served for two terms.
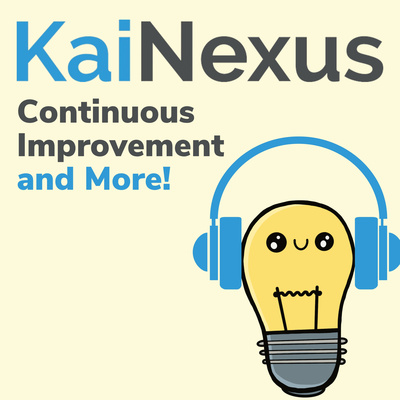
Panel: Cultivating a Culture of Learning from Mistakes
Learn more, get video, and more
Panelists:
Kym Guiliotti, Director of Product
Greg Jacobson, Co-founder & CEO
Maggie Millard, VP of Customer Experience
Linda Vicaro, Senior Lean Strategist
Moderated by:
Mark Graban, Senior Advisor
As KaiNexus co-founder and CEO Greg Jacobson, MD says, “You can’t have a culture of continuous improvement without learning from mistakes.”
Join us for a panel discussion featuring five KaiNexians who will share stories and reflections about cultivating a culture of psychological safety, where people feel safe to speak up about mistakes (or other opportunities for improvement) and also feel safe to try improvements and innovations.
The panel is being moderated by Mark Graban, who has been a senior advisor to KaiNexus since 2011. He loves talking about mistakes in his podcast "My Favorite Mistake" and also wrote (and published) a new book that includes stories from KaiNexus: "The Mistakes That Make Us: Cultivating a Culture of Learning and Innovation."
If you attend the live session, you'll also be able to ask questions about our lessons learned about cultivating a culture at KaiNexus and how this might benefit you, your team, and your organization.
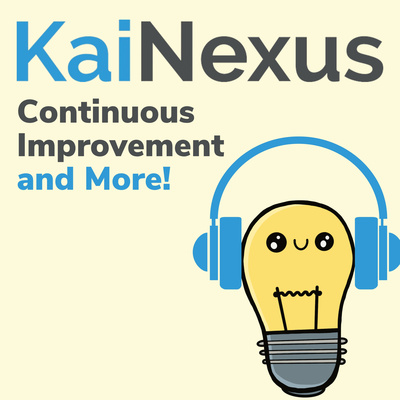
Webinar Panel Preview: Cultivating a Culture of Learning from Mistakes
Greg's podcast episode Mark's book: http://mistakesbook.com/ Panelists: Kym Guiliotti, Director of Product Greg Jacobson, Co-founder & CEO Maggie Millard, VP of Customer Experience Linda Vicaro, Senior Lean Strategist Moderated by: Mark Graban, Senior Advisor As KaiNexus co-founder and CEO Greg Jacobson, MD says, “You can’t have a culture of continuous improvement without learning from mistakes.” Join us for a panel discussion featuring five KaiNexians who will share stories and reflections about cultivating a culture of psychological safety, where people feel safe to speak up about mistakes (or other opportunities for improvement) and also feel safe to try improvements and innovations. The panel is being moderated by Mark Graban, who has been a senior advisor to KaiNexus since 2011. He loves talking about mistakes in his podcast "My Favorite Mistake" and also wrote (and published) a new book that includes stories from KaiNexus: "The Mistakes That Make Us: Cultivating a Culture of Learning and Innovation." If you attend the live session, you'll also be able to ask questions about our lessons learned about cultivating a culture at KaiNexus and how this might benefit you, your team, and your organization.
![Why Kindness is the Key to Lean Leadership [Webinar Recording]](https://d3t3ozftmdmh3i.cloudfront.net/production/podcast_uploaded_nologo400/1738065/1738065-1668561572420-df1dfb28a0f5.jpg)
Why Kindness is the Key to Lean Leadership [Webinar Recording]
Learn more and view the video: https://info.kainexus.com/continuous-improvement/why-kindness-is-the-key-to-lean-leadership/webinar/signup Presented by Karyn Ross, Founder of The New School for Kind Leaders People often think that lean is a kind way to work. But lean is a thing – and things aren’t kind or unkind – people are! In order for leaders to be able to develop people to work in lean ways, create, and innovate, they need to lead with kindness. In this webinar, you’ll learn about the Three Key Kind Leader Practices of Thinking, Speaking, and Acting Kindly, from Karyn Ross’s latest book "The Kind Leader: A Practical Guide to Eliminating Fear, Creating Trust and Leading with Kindness," and how and why they are the key to lean leadership.
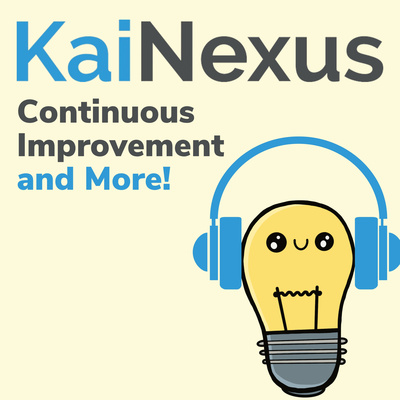
Remembering Masaaki Imai - "Kaizen" - Greg Jacobson & Mark Graban of KaiNexus
In this episode, Mark and Greg remember Masaaki Imai, who recently passed away at 92. They were both deeply influenced by Mr. Imai and his book "KAIZEN: The Key to Japan's Competitive Success." Without Greg being given this book by his Emergency Department leader, there would be no KaiNexus. Greg discusses the importance of the book to him and others -- and the broad influence it has had. Mark shares stories about meeting Mr. Imai (once in Seattle and twice in Japan) and some of the classic ideas -- that Kaizen means everybody improvement, everywhere improvement, every day improvement. See Mr. Imai talk about this: https://www.youtube.com/watch?v=WqKMlRJUAJk&ab_channel=KaizenInstitute-SouthAsia%26Africa They also discuss the connections between Kaizen and Lean books and practice -- and how Kaizen should be a core part of a Lean strategy, as it is at Toyota and other companies. Get the book KAIZEN on Amazon: https://amzn.to/3XAg2mz This approach should be the key to a hospital's success, or any organization's success -- not just manufacturing and not just in Japan. Mark's blog post about meeting Mr. Imai: https://www.leanblog.org/2012/06/meeting-mr-imai/ Greg's journal article about Kaizen: https://onlinelibrary.wiley.com/doi/full/10.1111/j.1553-2712.2009.00580.x
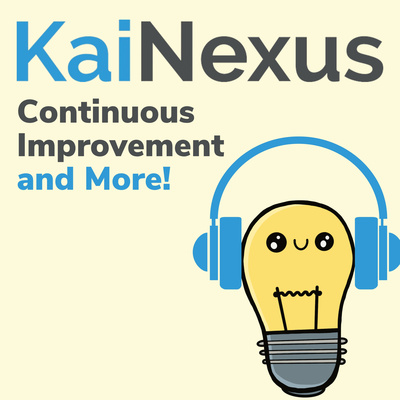
Kathryn Abbott:Why I Joined KaiNexus as a Customer Success Specialist
Mark Graban, a senior advisor with KaiNexus, is joined by Kathryn Abbott, who joined KaiNexus three months ago as a customer success specialist. In this episode, she shares her thoughts on what stood out to her about the culture and the people, as she was interviewing and how that's been reinforced by her first months at the company. She also shares a little bit about the way she helps customers in her role.
![[Preview] Why Kindness is the Key to Lean Leadership, Webinar with Karyn Ross](https://d3t3ozftmdmh3i.cloudfront.net/production/podcast_uploaded_nologo400/1738065/1738065-1668561572420-df1dfb28a0f5.jpg)
[Preview] Why Kindness is the Key to Lean Leadership, Webinar with Karyn Ross
Learn more and register Mark Graban, from KaiNexus, and Karyn Ross discuss her upcoming webinar. July 11 from 1:00 pm - 2:00 pm ET Presented by Karyn Ross, Founder of The New School for Kind Leaders People often think that lean is a kind way to work. But lean is a thing – and things aren’t kind or unkind – people are! In order for leaders to be able to develop people to work in lean ways, create, and innovate, they need to lead with kindness. In this webinar, you’ll learn about the Three Key Kind Leader Practices of Thinking, Speaking, and Acting Kindly, from Karyn Ross’s latest book "The Kind Leader: A Practical Guide to Eliminating Fear, Creating Trust and Leading with Kindness," and how and why they are the key to lean leadership. About the Presenter: Karyn Ross Karyn is on a mission to Help People Create a Better, Kinder World. An artist, internationally acclaimed speaker, award-winning author, consultant, coach and practitioner, Karyn travels the globe teaching people her unique system of combining creativity, continuous improvement and kindness to make a better world. As well as being the owner of KRC (Karyn Ross Consulting) Karyn is one of the Founding Mothers of Women in Lean – Our Table, a global group of more than seven hundred and fifty women lean practitioners. Karyn is also Founder and President of the Love and Kindness Project Foundation, a registered public charity and The New School for Kind Leaders. She has created both of these initiatives to help people around the world think, speak, act and lead more kindly. Karyn’s sixth book, The Kind Leader: A Practical Guide to Eliminating Fear, Creating Trust and Leading with Kindness is available for preorder. Karyn’s five other books are: How to Coach for Creativity and Service Excellence: A Lean Coaching Workbook, the Shingo-award winning The Toyota Way to Service Excellence: Lean Transformation in Service Organizations, I’ll Keep You Posted: 102 of My Reflections to Help You Start – and Deepen – Your Own Active Reflection Process, Think Kindly – Speak Kindly – Act Kindly: 366 Easy and Free Ideas You Can Use to Create a Kinder World…Starting Today, and Big Karma and Little Kosmo Help Each Other. Proceeds from books fund The Love and Kindness Project Foundation. When not traveling, Karyn spends time designing and sewing her own clothes! Follow Karyn on LinkedIn for a daily inspirational post about creativity, kindness and/or continuous improvement.
![[More Q&A] Psychological Safety as a Foundation for Continuous Improvement](https://d3t3ozftmdmh3i.cloudfront.net/production/podcast_uploaded_nologo400/1738065/1738065-1668561572420-df1dfb28a0f5.jpg)
[More Q&A] Psychological Safety as a Foundation for Continuous Improvement
Additional Q&A from Mark Graban's webinar...
![[Webinar] Psychological Safety as a Foundation for Continuous Improvement](https://d3t3ozftmdmh3i.cloudfront.net/production/podcast_uploaded_nologo400/1738065/1738065-1668561572420-df1dfb28a0f5.jpg)
[Webinar] Psychological Safety as a Foundation for Continuous Improvement
Learn more, get the video version, slides, and more
Presented by Mark Graban, KaiNexus Senior Advisor
Mark’s presentation will explore the connections between Psychological Safety and Continuous Improvement, using examples from Toyota, KaiNexus, and other companies.
Mark will explore how we can assess the current state of Psychological Safety in teams or across a broader organization. He’ll also discuss what leaders can do to help create conditions where employees feel safe enough to speak up about mistakes, problems, and improvement ideas.
![[Preview] Psychological Safety as a Foundation for Continuous Improvement](https://d3t3ozftmdmh3i.cloudfront.net/production/podcast_uploaded_nologo400/1738065/1738065-1668561572420-df1dfb28a0f5.jpg)
[Preview] Psychological Safety as a Foundation for Continuous Improvement
Today, Morgan Wright and Mark Graban preview Mark's upcoming webinar... "Psychological Safety as a Foundation for Continuous Improvement"
June 8 from 1:00 pm - 2:00 pm ET
Presented by Mark Graban, KaiNexus Senior Advisor
Mark’s presentation will explore the connections between Psychological Safety and Continuous Improvement, using examples from Toyota, KaiNexus, and other companies.
Mark will explore how we can assess the current state of Psychological Safety in teams or across a broader organization. He’ll also discuss what leaders can do to help create conditions where employees feel safe enough to speak up about mistakes, problems, and improvement ideas.
![[Webinar] Sustaining Continuous Improvement with Habit Science](https://d3t3ozftmdmh3i.cloudfront.net/production/podcast_uploaded_nologo400/1738065/1738065-1668561572420-df1dfb28a0f5.jpg)
[Webinar] Sustaining Continuous Improvement with Habit Science
More information, slides, and video recording
As presented May 11 from 1:00 pm - 2:00 pm ET
Presented by Morgan Wright (Customer Marketing Manager) and
Greg Jacobson, MD (co-founder and CEO), from KaiNexus.
Come join the final webinar in our three-part habit webinar series to learn how we sustain and maximize organizational habits in a continuous improvement culture. In this 1 hour webinar, we will review the highlights from the prior habits webinars, learn how you can design organizational habits, develop your Habit Loops by persona, and share stories of organizations who have seen incredible results from implementing habits.
![[Preview] Sustaining Continuous Improvement with Habit Science](https://d3t3ozftmdmh3i.cloudfront.net/production/podcast_uploaded_nologo400/1738065/1738065-1668561572420-df1dfb28a0f5.jpg)
[Preview] Sustaining Continuous Improvement with Habit Science
Morgan Wright, customer marketing manager at KaiNexus, joins Mark Graban, senior advisor at the company, to give a preview of this upcoming webinar, the third in a series about "habit loops": Sustaining Continuous Improvement with Habit Science
Part 2 About the webinar: Come join the final webinar in our three-part habit webinar series to learn how we sustain and maximize organizational habits in a continuous improvement culture. In this 1 hour webinar, we will review the highlights from the prior habits webinars, learn how you can design organizational habits, develop your Habit Loops by persona, and share stories of organizations who have seen incredible results from implementing habits. About the Presenters: Morgan Wright Customer Marketing Manager, KaiNexus Greg Jacobson Co-Founder & CEO, KaiNexus
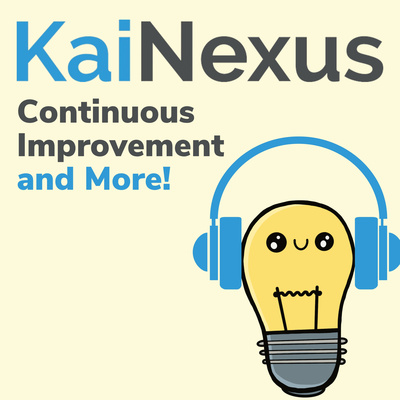
Elise Miller - Why Did You Join KaiNexus? The Culture, the People, and Getting to Be Yourself
Elise Miller, Manager of Solutions Engineering at KaiNexus, has a chat with Mark Graban about why she joined the company in 2020, why the culture appeals to her, and how her role has evolved from Solutions Engineer to the Manager of that now-larger and growing team.
Learn more about KaiNexus: http://kainexus.com/
![Deepen Your Lean Leadership Skills with Brain Science [Webinar by Elisabeth Swan]](https://d3t3ozftmdmh3i.cloudfront.net/production/podcast_uploaded_nologo400/1738065/1738065-1668561572420-df1dfb28a0f5.jpg)
Deepen Your Lean Leadership Skills with Brain Science [Webinar by Elisabeth Swan]
Learn more, get slides, see the video
Presented by Elisabeth Swan
We often underestimate our influence on others. We fail to recognize the impact we have on people, their work, their ability to solve problems, and thrive. Whether we hold formal leadership positions or not, we all have the power to affect those around us. However, the way we think, speak, and act may not always bring out the best in ourselves or those we interact with. This can lead to missed opportunities, strained relationships, and less-than-ideal outcomes.
Come join this 1-hour webinar to get insights on how to use the reality of how our minds work to address those people-centric challenges and become a force for good. You’ll get tools to enhance your ability to help people navigate change and make a lasting impact on the organization and those around you.
Elisabeth has consulted in the business process performance industry for over 30 years. Her experience spans from helping local non-profits expand their reach to guiding Fortune 100 companies through Lean Transformations. She has trained and mentored thousands of people in improvement projects generating millions in savings. She has deep experience coaching problem solvers and facilitating leadership retreats, strategic planning sessions, process walks, and kaizen events.
Elisabeth is the Co-Designer and Lead Instructor for the Lean Six Sigma Leadership Course at University of California, San Diego (UCSD). She is a co-founder of Just-in-Time Café, and co-host of the Just-in-Time Café podcast. She co-wrote The Problem Solver’s Toolkit: A Surprisingly Simple Guide to Your Lean Six Sigma Journey, and her latest book is, Picture Yourself a Leader: Illustrated Micro-Lessons in Navigating Change.
![[Preview] Deepen Your Lean Leadership Skills with Brain Science](https://d3t3ozftmdmh3i.cloudfront.net/production/podcast_uploaded_nologo400/1738065/1738065-1668561572420-df1dfb28a0f5.jpg)
[Preview] Deepen Your Lean Leadership Skills with Brain Science
Register for the webinar or the recording
This episode previews Elisabeth Swan's upcoming webinar, hosted by KaiNexus and Mark Graban. Elisabeth joins Mark here to discuss it.
April 18 from 1:00 pm - 2:00 pm ET
Enter to win one of 3 signed copies of her new book, Picture Yourself a Leader, by sharing about the webinar on LinkedIn with the hashtag #KaiNexus.
Presented by Elisabeth Swan
We often underestimate our influence on others. We fail to recognize the impact we have on people, their work, their ability to solve problems, and thrive. Whether we hold formal leadership positions or not, we all have the power to affect those around us. However, the way we think, speak, and act may not always bring out the best in ourselves or those we interact with. This can lead to missed opportunities, strained relationships, and less-than-ideal outcomes.
Come join this 1-hour webinar to get insights on how to use the reality of how our minds work to address those people-centric challenges and become a force for good. You’ll get tools to enhance your ability to help people navigate change and make a lasting impact on the organization and those around you.
Elisabeth has consulted in the business process performance industry for over 30 years. Her experience spans from helping local non-profits expand their reach to guiding Fortune 100 companies through Lean Transformations. She has trained and mentored thousands of people in improvement projects generating millions in savings. She has deep experience coaching problem solvers and facilitating leadership retreats, strategic planning sessions, process walks, and kaizen events.
Elisabeth is the Co-Designer and Lead Instructor for the Lean Six Sigma Leadership Course at University of California, San Diego (UCSD). She is a co-founder of Just-in-Time Café, and co-host of the Just-in-Time Café podcast. She co-wrote The Problem Solver’s Toolkit: A Surprisingly Simple Guide to Your Lean Six Sigma Journey, and her latest book is, Picture Yourself a Leader: Illustrated Micro-Lessons in Navigating Change.